why modular
The benefits of offsite construction are both project and societal, with volumetric modular being the most powerful in addressing big issues like affordable housing and climate change.
The why OF volumetric modular
The "Full Meal Deal" of Offsite Construction
Volumetric modular is the process of constructing six-sided modules in an offsite, climate-controlled facility and then transporting, stacking and joining the modules at the jobsite to create a finished building. With 75 to 90% of a project’s scope combined and completed within one highly controlled and precise manufacturing process, an owner can experience many benefits. Find out why more people than ever are turning to volumetric modular and how RISE, through team collaboration and excellent planning, ensures our clients realize its full power.
BENEFITS OF MODULAR
The saying, time is money has never been truer than in construction! Volumetric modular has been proven to be 30 to 50% faster than traditional construction methods. Here’s why:
- Modules are built within our manufacturing facility concurrently with site activities. Sequencing of construction is reduced. Modules can be set in a matter of days or weeks.
- Constructing modules inside a factory adds certainty. Construction can take place every day, regardless of weather conditions.
- Production is more efficient. Materials are brought to each station precut, and employees are not fighting adverse site or weather conditions.
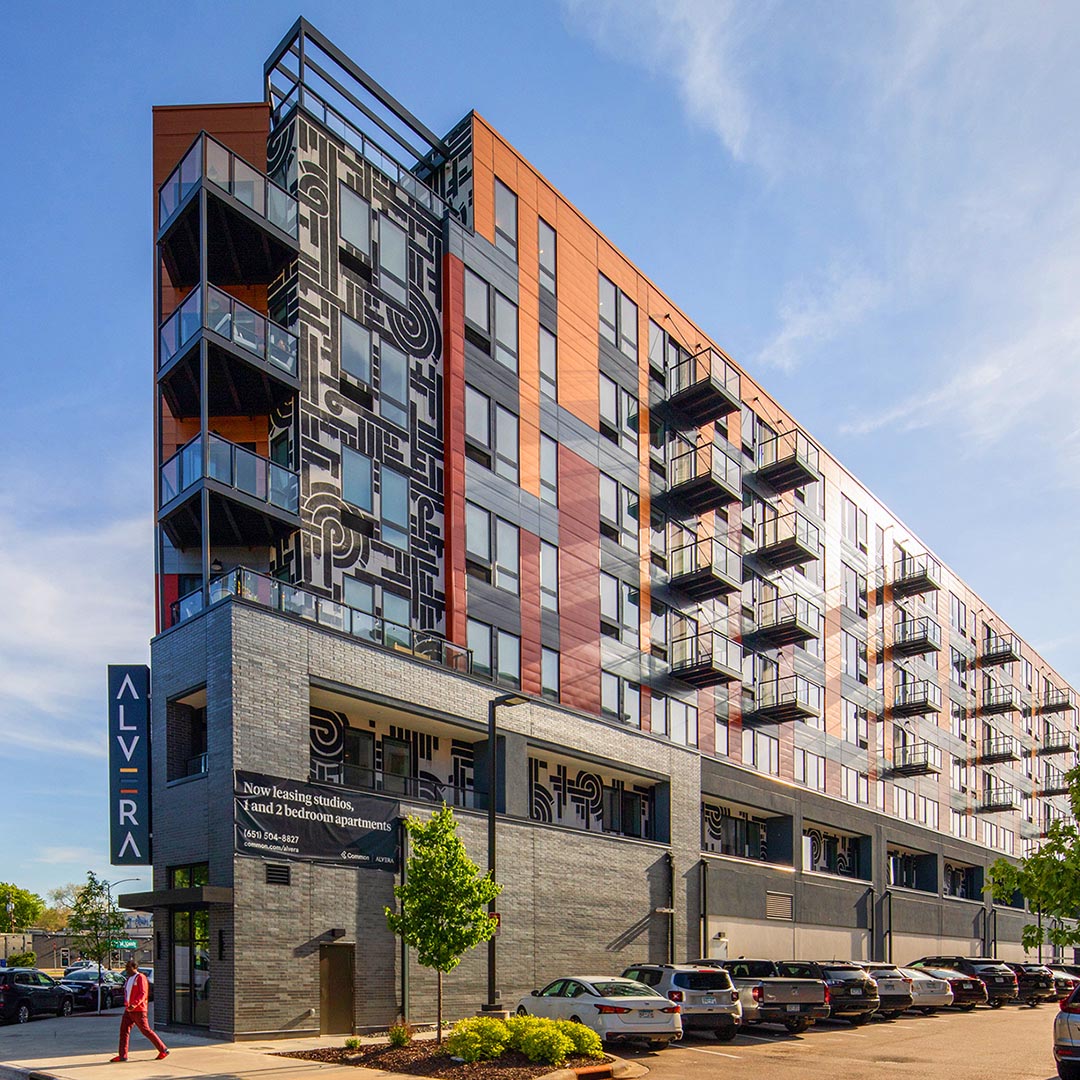
alvera apartments
At 193 units, if constructed traditionally, Alvera Apartments would have taken 18 to 24 months to complete. With our modules, this project — one of North America’s most complex woodframed modular projects — was completed in 13 months.
The biggest cost advantage for volumetric modular is control and consistency. Because design decisions are made earlier in an offsite process versus traditional, the cost at the beginning of construction is the cost at the end of construction.
- Clients make design decisions on items such as flooring, cabinetry, appliances and lighting packages prior to manufacturing, so there are no surprises during the final installation. This means far fewer change orders.
- Time is money and with more than 150 employees arriving daily to the manufacturing facility, work proceeds, rain or shine. On a traditional project, if one sub fails to deliver or show up, there’s a domino effect that can mean wasted labor costs, time delays or price increases.
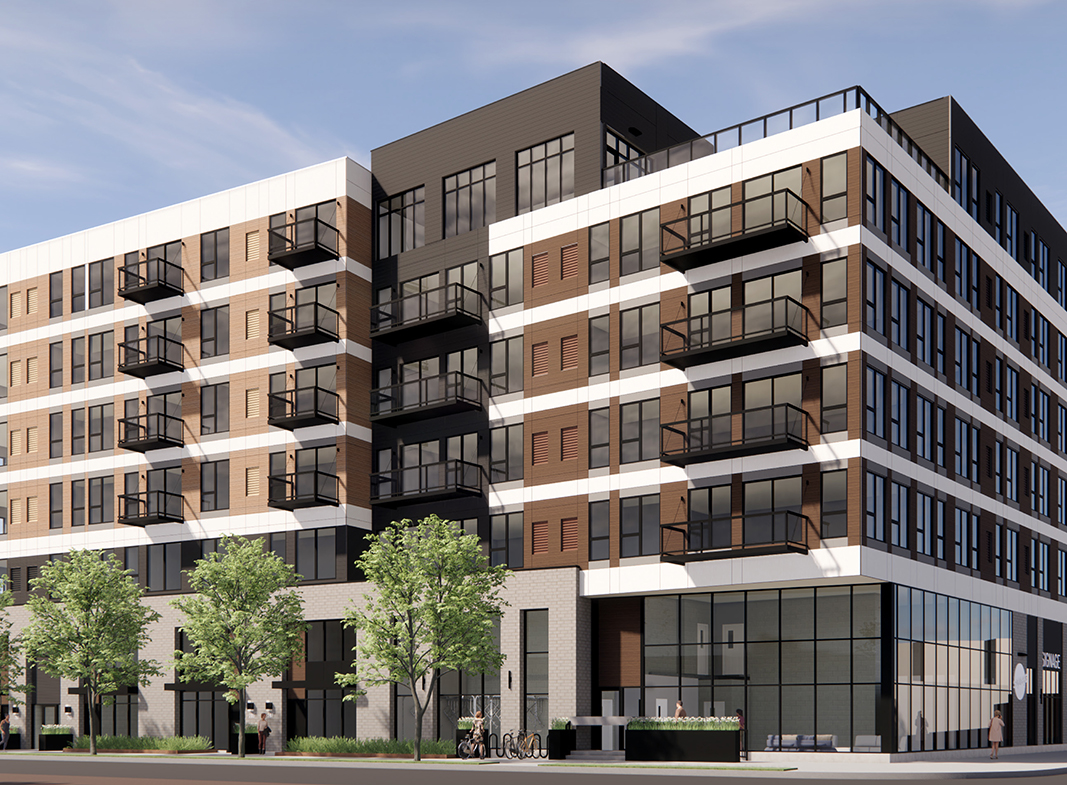
Glenwood APARTMENTS
Combining volumetric modular with Enterprise Community Partners’ Opportunity Fund, Glenwood Apartments can bring more than 50% of its units to those with an 80% area median income and 10-% of those at a 60% area median income WITHOUT public assistance.
Our manufacturing facility is 100% climate-controlled and highly automated. Work is completed without the effects of weather or the impact of dirt and debris.
- Our assembly-line approach allows us to fine-tune our work and deliver a level of precision unavailable in field assembly.
- We work in ergonomic stations where materials are kitted and brought directly to each station.
- Quality is checked on each module before progressing to the next station.
- Because modules are trucked long distances and then moved by crane onto a foundation, they are built to be extremely structurally sound.
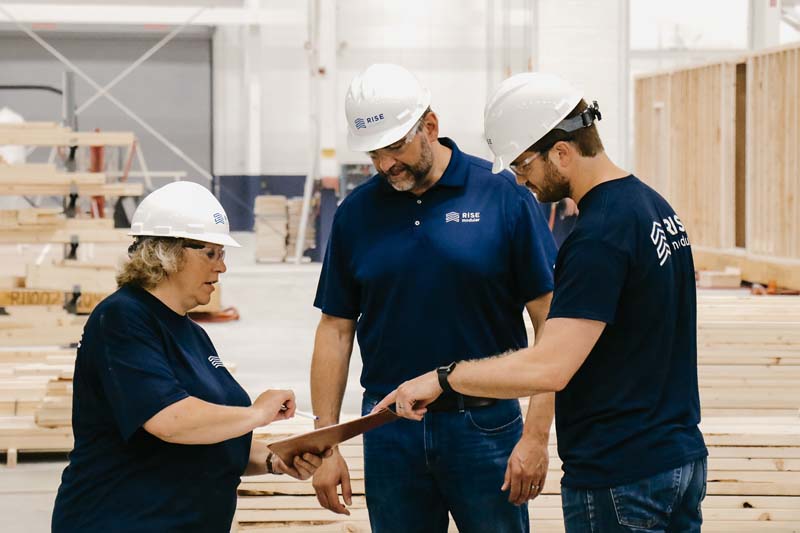
our modular process
Quality is at the forefront of our manufacturing process and checked to a level of detail unachievable in the uncontrolled conditions of a jobsite. Because each module is a six-sided structure, each apartment or room is more soundproof and airtight!
Offsite construction optimizes construction materials purchasing and usage while minimizing onsite waste and offering a higher quality product to the owner/developer.
- Up to a 90% reduction in waste can be achieved using modular construction, according to the UK group WRAP.
- Waste is minimized on items such as wood pallets, shrink wrap, cardboard, plasterboard, timber, concrete bricks, and cement.
- With 75 to 90% of the project built offsite, vehicular traffic and equipment needs are significantly reduced and the impact on the surrounding environment is minimized.
- Volumetric modules are engineered and built to withstand transport and create tighter, more energy-efficient builds.
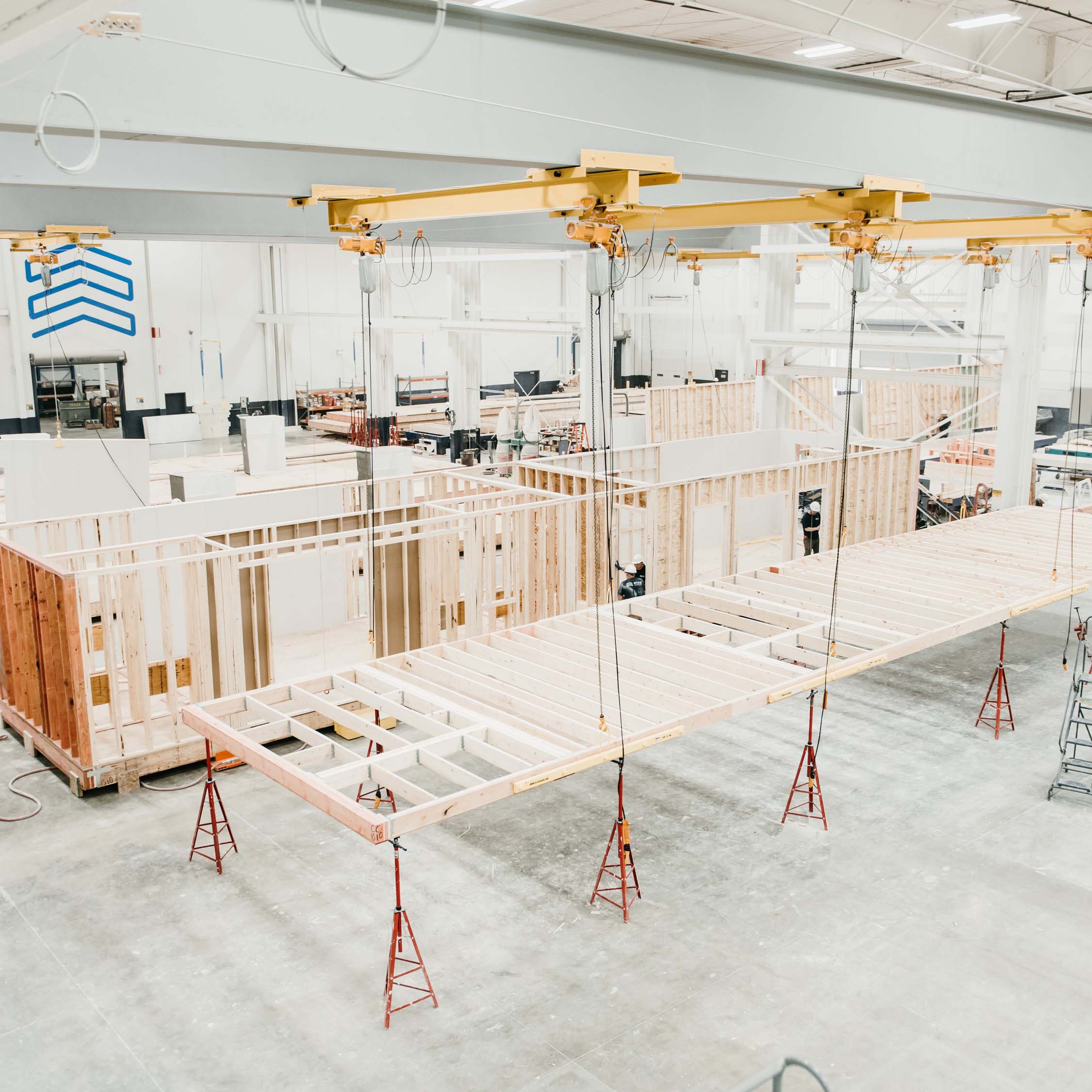
our modular process
According to a new study from the University of Cambridge and Edinburgh Napier University, buildings constructed utilizing volumetric modular manufacturing can produce 41-45% less CO2 than traditional construction.
- The need for fall protection is minimized. Typically employees work at their level and are not going up and down multiple floors or scaffolding.
- Work is performed at stations and flows through the factory without congestion, confusion or traffic.
- Employees do not have to fight the elements or wear bulky gear. Our team is in t-shirts year-round where it’s always 70 degrees.

our modular process
Our manufacturing facility is designed to work with employees…heavy walls are lifted with cranes, and mods move through the plant with just three people. RISE also cross-trains employees, so there is never anyone untrained on the assembly line.
Because 75 to 90% of construction is completed offsite, neighbors do not have to deal with a prolonged construction timeline filled with noise, dust, traffic, and constant deliveries that take up valuable street space and driveways.
- Road closures are limited to when the mods are being set on a project site, typically 1-4 weeks. A traditional build would require road closures of up to 1-2 years.
- There are fewer workers onsite therefore fewer people parking on neighborhood streets, lighter traffic and minimized noise pollution.
- There are far fewer truck deliveries and fewer beep-beeps from semi-trailers backing up at 6am.
- Since a building goes from a concrete slab to a completely enclosed structure in a matter of days versus months, the jobsite is safer and less likely to attract crime.
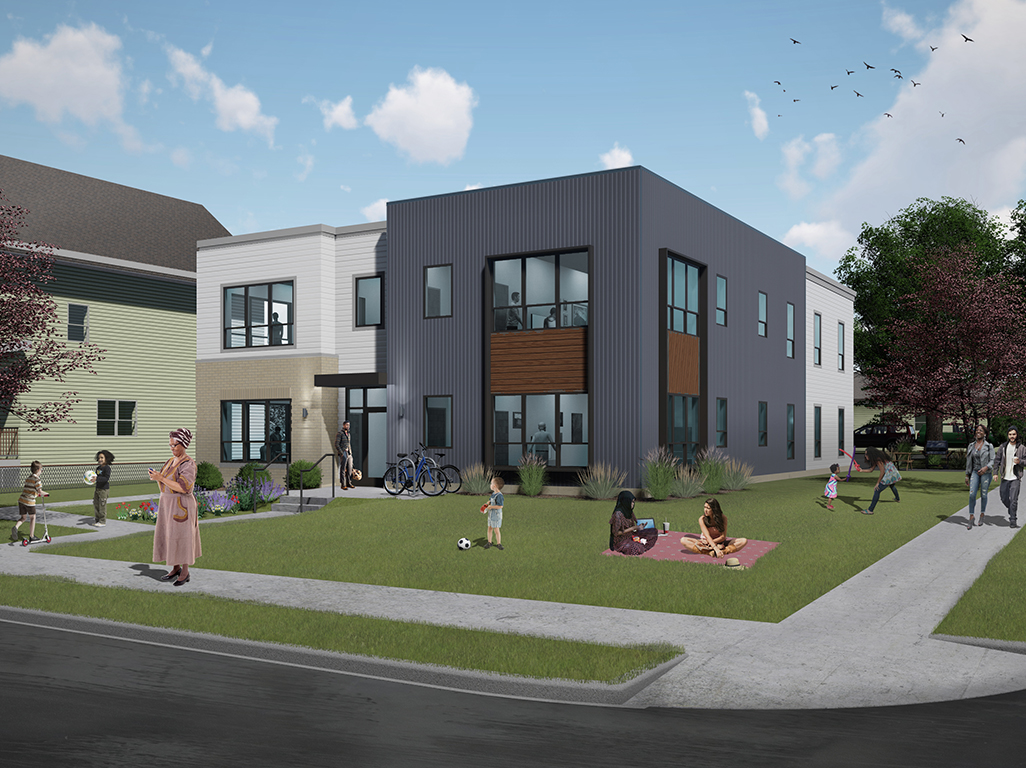
mpha family expansion plan
The Minneapolis Public Housing Authority is taking on an ambitious 16-building, scattered-site development to improve existing affordable housing properties and make much-needed additions across Minneapolis. Utilizing our modular process, the four- to six-unit buildings will take only 1 or 2 days to set on these tight, urban residential neighborhood sites.
RISE PROCESS
How It All Comes Together
The volumetric modular difference is the process: the concurrent coordination of onsite and offsite activities to achieve the best results. The RISE Modular difference is how our integrated team of experts utilizes the best in technology and advanced manufacturing practices to guide you through that process and maximize your success.